Abstract: The influence of different heat treatment processes on the performance of ZG06Cr13Ni4Mo material was studied. The test shows that after heat treatment at 1 010℃ normalizing + 605℃ primary tempering + 580℃ secondary tempering, the material reaches the best performance index. Its structure is low-carbon martensite + reverse transformation austenite, with high strength, low-temperature toughness and suitable hardness. It meets the product performance requirements in the application of large blade casting heat treatment production.
Keywords: ZG06Cr13NI4Mo; martensitic stainless steel; blade
Large blades are key parts in hydropower turbines. The service conditions of the parts are relatively harsh, and they are subjected to high-pressure water flow impact, wear and erosion for a long time. The material is selected from ZG06Cr13Ni4Mo martensitic stainless steel with good comprehensive mechanical properties and corrosion resistance. With the development of hydropower and related castings towards large-scale, higher requirements are put forward for the performance of stainless steel materials such as ZG06Cr13Ni4Mo. To this end, combined with the production trial of ZG06C r13N i4M o large blades of a domestic hydropower equipment enterprise, through internal control of the material chemical composition, heat treatment process comparison test and test result analysis, the optimized single normalizing + double tempering heat treatment process of ZG06C r13N i4M o stainless steel material was determined to produce castings that meet high performance requirements.
1 Internal control of chemical composition
ZG06C r13N i4M o material is high-strength martensitic stainless steel, which is required to have high mechanical properties and good low-temperature impact toughness. In order to improve the performance of the material, the chemical composition was internally controlled, requiring w (C) ≤ 0.04%, w (P) ≤ 0.025%, w (S) ≤ 0.08%, and the gas content was controlled. Table 1 shows the chemical composition range of the material internal control and the analysis results of the chemical composition of the sample, and Table 2 shows the internal control requirements of the material gas content and the analysis results of the sample gas content.
Table 1 Chemical composition (mass fraction, %)
element |
C |
Mn |
Si |
P |
S |
Ni |
Cr |
Mo |
Cu |
Al |
standard requirement |
≤0.06 |
≤1.0 |
≤0.80 |
≤0.035 |
≤0.025 |
3.5-5.0 |
11.5-13.5 |
0.4-1.0 |
≤0.5 |
|
Ingredients Internal Control |
≤0.04 |
0.6-0.9 |
1.4-0.7 |
≤0.025 |
≤0.008 |
4.0-5.0 |
12.0-13.0 |
0.5-0.7 |
≤0.5 |
≤0.040 |
Analyze the results |
0.023 |
1.0 |
0.57 |
0.013 |
0.005 |
4.61 |
13.0 |
0.56 |
0.02 |
0.035 |
Table 2 Gas content (ppm)
gas |
H |
O |
N |
Internal control requirements |
≤2.5 |
≤80 |
≤150 |
Analyze the results |
1.69 |
68.6 |
119.3 |
The ZG06C r13N i4M o material was smelted in a 30 t electric furnace, refined in a 25T LF furnace for alloying, adjusting the composition and temperature, and decarburized and degassed in a 25T VOD furnace, thereby obtaining molten steel with ultra-low carbon, uniform composition, high purity, and low harmful gas content. Finally, aluminum wire was used for final deoxidation to reduce the oxygen content in the molten steel and further refine the grains.
2 Heat treatment process test
2.1 Test plan
The casting body was used as the test body, the test block size was 70mm× 70mm×230mm, and the preliminary heat treatment was softening annealing. After consulting the literature, the heat treatment process parameters selected were: normalizing temperature 1 010℃, primary tempering temperatures 590℃, 605℃, 620℃, secondary tempering temperature 580℃, and different tempering processes were used for comparative tests. The test plan is shown in Table 3.
Table 3 Heat treatment test plan
Trial plan |
Heat treatment test process |
Pilot projects |
A1 |
1 010℃Normalizing+620℃Tempering |
Tensile properties Impact toughness Hardness HB Bending properties Microstructure |
A2 |
1 010℃Normalizing+620℃Tempering+580℃Tempering |
|
B1 |
1 010℃Normalizing+620℃Tempering |
|
B2 |
1 010℃Normalizing+620℃Tempering+580℃Tempering |
|
C1 |
1 010℃Normalizing+620℃Tempering |
|
C2 |
1 010℃Normalizing+620℃Tempering+580℃Tempering |
2.2 Analysis of test results
2.2.1 Chemical composition analysis
From the analysis results of chemical composition and gas content in Table 1 and Table 2, the main elements and gas content are in line with the optimized composition control range.
2.2.2 Analysis of performance test results
After heat treatment according to different test schemes, mechanical properties comparison tests were carried out in accordance with GB/T228.1-2010, GB/T229-2007, and GB/T231.1-2009 standards. The experimental results are shown in Table 4 and Table 5.
Table 4 Mechanical properties analysis of different heat treatment process schemes
Trial plan |
Rp0.2/Mpa |
Rm/Mpa |
A/% |
Z/% |
AKV/J(0℃) |
Hardness value HBW |
standard |
≥550 |
≥750 |
≥15 |
≥35 |
≥50 |
210~290 |
A1 |
526 |
786 |
21.5 |
71 |
168、160、168 |
247 |
A2 |
572 |
809 |
26 |
71 |
142、143、139 |
247 |
B1 |
588 |
811 |
21.5 |
71 |
153、144、156 |
250 |
B2 |
687 |
851 |
23 |
71 |
172、165、176 |
268 |
C1 |
650 |
806 |
23 |
71 |
147、152、156 |
247 |
C2 |
664 |
842 |
23.5 |
70 |
147、141、139 |
263 |
Table 5 Bending test
Trial plan |
Bending test(d=25,a=90°) |
assessment |
B1 |
Crack5.2×1.2mm |
Failure |
B2 |
No cracks |
qualified |
From the comparison and analysis of mechanical properties: (1) Normalizing + tempering heat treatment, the material can obtain better mechanical properties, indicating that the material has good hardenability. (2) After normalizing heat treatment, the yield strength and plasticity (elongation) of the double tempering are improved compared with the single tempering. (3) From the bending performance inspection and analysis, the bending performance of the B1 normalizing + single tempering test process is unqualified, and the bending test performance of the B2 test process after double tempering is qualified. (4) From the comparison of the test results of 6 different tempering temperatures, the B2 process scheme of 1 010℃ normalizing + 605℃ single tempering + 580℃ secondary tempering has the best mechanical properties, with a yield strength of 687MPa, an elongation of 23%, an impact toughness of more than 160J at 0℃, a moderate hardness of 268HB, and a qualified bending performance, all meeting the performance requirements of the material.
2.2.3 Metallographic structure analysis
The metallographic structure of material B1 and B2 test processes was analyzed according to GB/T13298-1991 standard. Figure 1 shows the metallographic structure of normalizing + 605℃ first tempering, and Figure 2 shows the metallographic structure of normalizing + first tempering + second tempering. From the metallographic inspection and analysis, the main structure of ZG06C r13N i4M o after heat treatment is low-carbon lath martensite + reversed austenite. From the metallographic structure analysis, the lath martensite bundles of the material after the first tempering are thicker and longer. After the second tempering, the matrix structure changes slightly, the martensite structure is also slightly refined, and the structure is more uniform; in terms of performance, the yield strength and plasticity are improved to a certain extent.
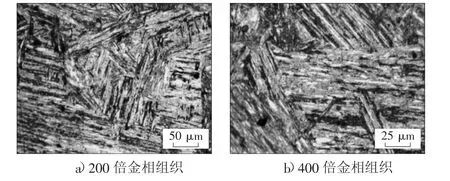
Figure 1 ZG06Cr13Ni4Mo normalizing + one tempering microstructure
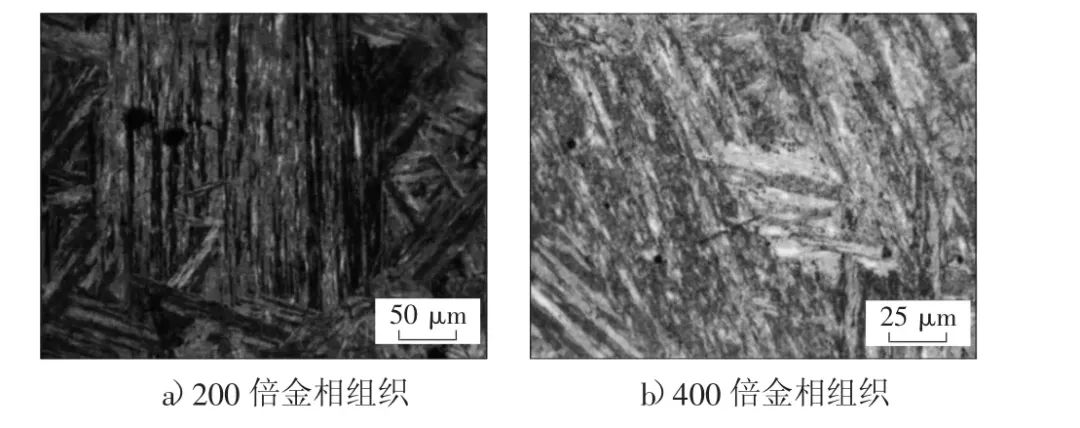
Figure 2 ZG06Cr13Ni4Mo normalizing + twice tempering metallographic structure
2.2.4 Analysis of test results
1) The test confirmed that ZG06C r13N i4M o material has good hardenability. Through normalizing + tempering heat treatment, the material can obtain good mechanical properties; the yield strength and plastic properties (elongation) of two temperings after normalizing heat treatment are much higher than those of one tempering.
2) The test analysis proves that the structure of ZG06C r13N i4M o after normalizing is martensite, and the structure after tempering is low-carbon lath tempered martensite + reversed austenite. The reversed austenite in the tempered structure has high thermal stability and has a significant effect on the mechanical properties, impact properties and casting and welding process properties of the material. Therefore, the material has high strength, high plastic toughness, appropriate hardness, good crack resistance and good casting and welding properties after heat treatment.
3) Analyze the reasons for the improvement of the secondary tempering performance of ZG06C r13N i4M o. After normalizing, heating and heat preservation, ZG06C r13N i4M o forms fine-grained austenite after austenitization, and then transforms into low-carbon martensite after rapid cooling. In the first tempering, the supersaturated carbon in the martensite precipitates in the form of carbides, thereby reducing the strength of the material and improving the plasticity and toughness of the material. Due to the high temperature of the first tempering, the first tempering produces extremely fine reverse austenite in addition to the tempered martensite. These reverse austenites are partially transformed into martensite during tempering cooling, providing conditions for the nucleation and growth of stable reverse austenite generated again during the secondary tempering process. The purpose of secondary tempering is to obtain enough stable reverse austenite. These reverse austenites can undergo phase transformation during plastic deformation, thereby improving the strength and plasticity of the material. Due to limited conditions, it is impossible to observe and analyze the reverse austenite, so this experiment should take the mechanical properties and microstructure as the main research objects for comparative analysis.
3 Production Application
ZG06C r13N i4M o is a high-strength stainless steel cast steel material with excellent performance. When the actual production of blades is carried out, the chemical composition and internal control requirements determined by the experiment, and the heat treatment process of secondary normalizing + tempering are used for production. The heat treatment process is shown in Figure 3. At present, the production of 10 large hydropower blades has been completed, and the performance has all met the user's requirements. They have passed the user's re-inspection and have received good evaluation.
For the characteristics of complex curved blades, large contour dimensions, thick shaft heads, and easy deformation and cracking, some process measures need to be taken in the heat treatment process:
1) The shaft head is downward and the blade is upward. The furnace loading scheme is adopted to facilitate minimum deformation, as shown in Figure 4;
2) Ensure that there is a large enough gap between the castings and between the castings and the pad iron bottom plate to ensure cooling, and ensure that the thick shaft head meets the ultrasonic detection requirements;
3) The heating stage of the workpiece is segmented multiple times to minimize the organizational stress of the casting during the heating process to prevent cracking.
The implementation of the above heat treatment measures ensures the heat treatment quality of the blade.
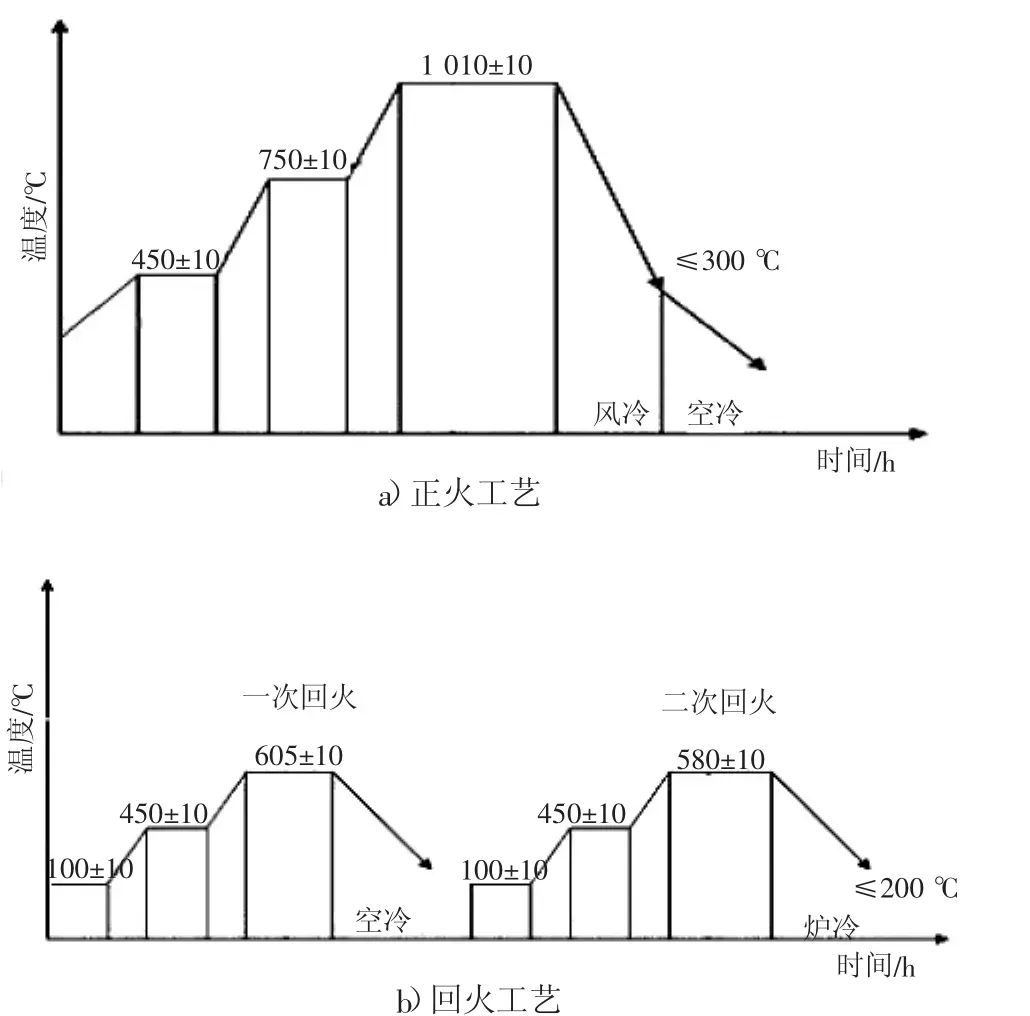
Figure 3 ZG06Cr13Ni4Mo blade heat treatment process
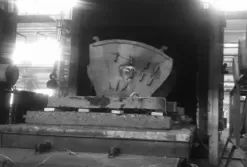
Figure 4 Blade heat treatment process furnace loading scheme
4 Conclusions
1) Based on the internal control of the chemical composition of the material, through the test of the heat treatment process, it is determined that the heat treatment process of ZG06C r13N i4M o high-strength stainless steel material is a heat treatment process of 1 010℃ normalizing + 605℃ primary tempering + 580℃ secondary tempering, which can ensure that the mechanical properties, low-temperature impact properties and cold bending properties of the casting material meet the standard requirements.
2) ZG06C r13N i4M o material has good hardenability. The structure after normalizing + twice tempering heat treatment is a low-carbon lath martensite + reverse austenite with good performance, which has high strength, high plastic toughness, appropriate hardness, good crack resistance and good casting and welding performance.
3) The heat treatment scheme of normalizing + twice tempering determined by the experiment is applied to the heat treatment process production of large blades, and the material properties all meet the user's standard requirements.
Post time: Jun-28-2024